Selecting Your Solar System
Sizing your system
How much of your utility-supplied energy do you want to reduce? Not sure? Keep reading!
A common residential size in Florida is a five-kilowatt (kW) solar system. A five-kW system can potentially produce up to 4,250 watts (there is typically a 15% loss converting DC power to AC power).
Per Florida Administrative Code, systems greater than ten kW (AC) require owners to hold a $1 million liability insurance policy.
Still not sure what size system you want? Find a qualified contractor to help you – but contact a SECO Solar Expert first.
Do the math
- Example: SECO Energy charges 10 cents ($.10) per kWh
- An HVAC system consumes 4,000 watts (4 kW) operating for 10 hours a day
- HVAC operation (10 hours) will cost 4 kW x 10 hours = 40 kWh x 10 cents per kWh = $4.00
- For a 30-day period, your HVAC will cost $4.00 per day x 30 days = $120
For demonstration purposes only – kilowatt hour (kWh) rates are subject to change.
Panel Types
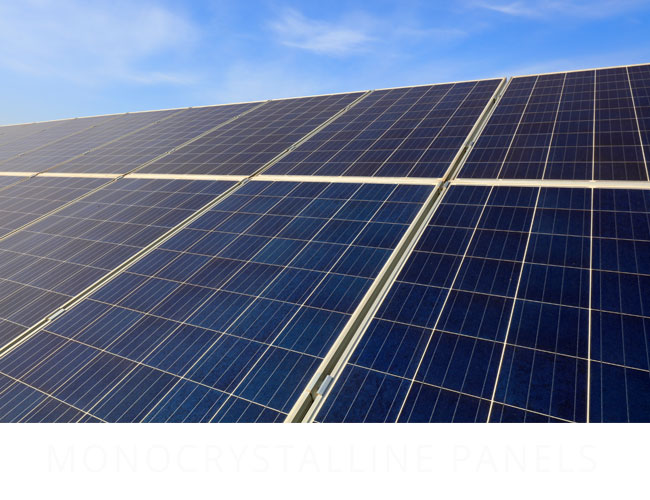
Monocrystalline Panels
Solar cells made of monocrystalline silicone are recognizable by an even coloring and uniform look. These cells are made out of cylindrical silicon ingots. To optimize performance and lower costs of a cell, four sides are cut out of the ingots to make wafers, giving these panels their characteristic look.
Advantages
• Monocrystalline panels have the highest efficiency rates since they are made out of the highest-grade silicon.
• Since these solar panels yield the highest power outputs, they also require the least amount of space compared to other types.
• Monocrystalline solar panels produce up to four times the amount of electricity as thin-film panels.
• Monocrystalline solar panels have the longest lifespan. Most manufacturers put a 25-year warranty on these panels.
• These tend to perform better than similarly rated polycrystalline solar panels at low-light conditions.
Disadvantages
• Monocrystalline solar panels are the most expensive. From a financial standpoint, a solar panel that is made of polycrystalline silicon (and in some cases thin-film) can be a better choice for some homeowners.
• If the panel is partially covered with shade or dirt, the entire circuit can break down. Using micro-inverters will ensure that the entire array is not affected by one panel’s shading.
• A special process is used to produce monocrystalline silicon, resulting in large cylindrical ingots. Four sides are cut out of the ingots to make wafers. A significant amount of the silicon ends up waste.
• Monocrystalline solar panels tend to be more efficient in warm weather. Performance suffers as temperature goes up, but less so than polycrystalline solar panels.
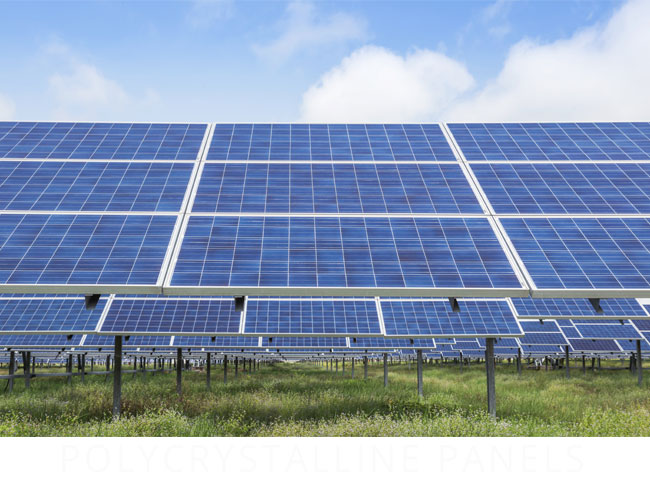
Polycrystalline Panels
The first solar panels based on polycrystalline silicon were introduced to the market in 1981. Unlike monocrystalline-based solar panels, polycrystalline panels do not require the Czochralski process (a special manufacturing process). Raw silicon is melted and poured into a square mold, which is cooled and cut into square wafers.
Advantages
• The process used to make polycrystalline silicon is simple and costs less.
• The amount of waste silicon is less compared to monocrystalline.
• Polycrystalline solar panels tend to have slightly lower heat tolerance than monocrystalline panels. This technically means that they perform slightly worse in high temperatures.
Disadvantages
• The efficiency of polycrystalline-based solar panels is typically 13-16%. Because of lower silicon purity, polycrystalline panels are not quite as efficient as monocrystalline panels.
• These panels carry lower space-efficiency. You need to cover a larger surface to output the same power as you would with a panel made of monocrystalline silicon.
• Monocrystalline and thin-film solar panels tend to be more aesthetically pleasing since they have a more uniform look compared to the speckled blue color of polycrystalline silicon.
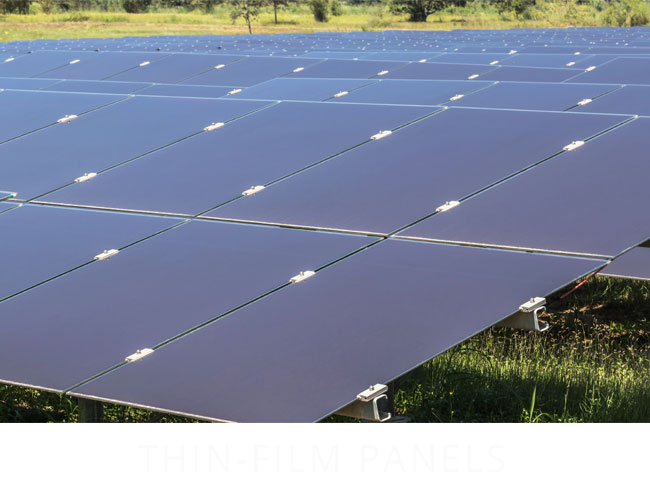
Thin-film Panels
Depositing one or several thin layers of photovoltaic material onto a substrate is how thin-film solar cells are manufactured. They are also known as thin-film photovoltaic cells (TFPV). The different types of thin-film solar cells are categorized by which material is deposited onto the substrate:
• Amorphous silicon (a-Si)
• Cadmium telluride (CdTe)
• Copper indium gallium selenide (CIS/CIGS)
• Organic photovoltaic cells (OPC)
Depending on the technology, thin-film module prototypes have reached efficiencies between 7–13% and production modules operate at about 9%. Future module efficiencies are expected to climb close to about 10–16%.
Advantages
• Mass-production is simple and makes thin film potentially cheaper to manufacture than crystalline-based solar cells.
• These panels’ homogenous appearance makes them more aesthetically appealing.
• Thin film panels are flexible, which opens up many new potential applications.
• High temperatures and shading have less impact on performance.
• In situations where space is not an issue, thin-film solar panels make sense.
Disadvantages
• Thin-film solar panels are less useful for in most residential situations. They are cheap, but they also require a lot of space.
• Low space-efficiency also means that the costs of PV-equipment (e.g. support structures and cables) will increase.
• Thin-film solar panels tend to degrade faster than mono- and polycrystalline panels, which is why they typically have a shorter warranty.
Insurance Regulations
- Tier 1 (Generating Facilities ≤ 10 kW Alternating Current) – Per the Florida Administrative Code: “The investor-owned utility shall not require liability insurance for Tier 1. The investor-owned utility may include in the Interconnection Agreement a recommendation that Tier 1 customers carry an appropriate level of liability insurance.”
- Tier 2 (Generating Facilities ˃ 10 kW and ≤ 100 kW Alternating Current) – Per the Florida Administrative Code: “A requirement for general liability insurance for personal and property damage, or sufficient guarantee and proof of self-insurance, in the amount of no more than $1 million for Tier 2.”
- Tier 3 (Generating Facilities ˃ 100 KW and ≤ 2 MW Alternating Current) – Per the Florida Administrative Code: “A requirement for general liability insurance for personal and property damage, or sufficient guarantee and proof of self-insurance, in the amount of no more than $2 million for Tier 3.”
Inverter Selection
Inverter choice is important. Inverters convert DC power produced by solar panels to the AC power used in your home or returned to the grid. There are three types of inverters:
STRING OR CENTRAL INVERTERS
String or central inverters are the most common and the most cost-effective. Panels are arranged in a group called a “string” attached to a single inverter. Use string or central inverters only if no shade is present year-round, otherwise production is reduced.
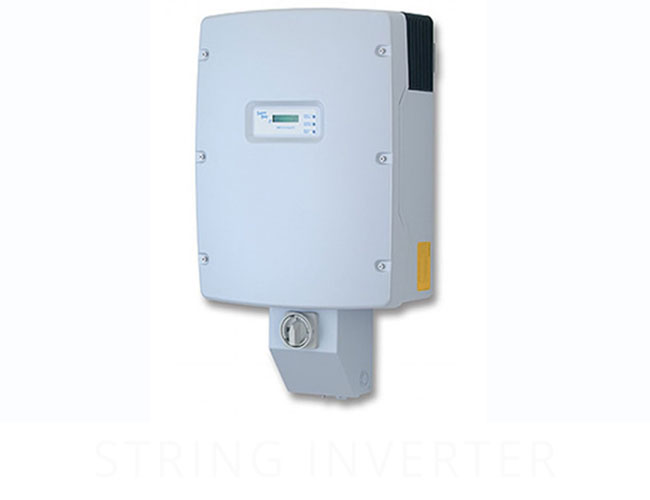
MICRO-INVERTERS
Micro-inverters are installed on each panel and DC to AC power is converted at each panel. All panels should operate at full capacity if conditions are optimal. Owners are able to monitor the production of each panel. This is a costly option as it requires the purchase of an inverter for each panel.
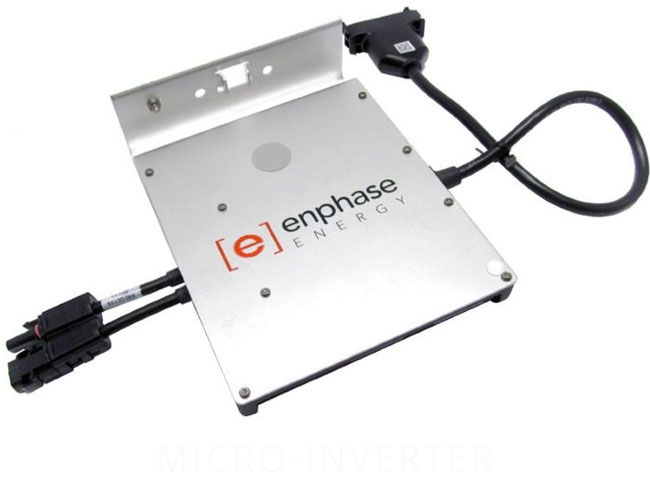
POWER OPTIMIZERS
Power optimizers are less expensive than micro-inverters and are installed at each panel. Power optimizers do not convert DC to AC power at the panel. They send DC power to a single string inverter allowing for efficiency and monitoring.
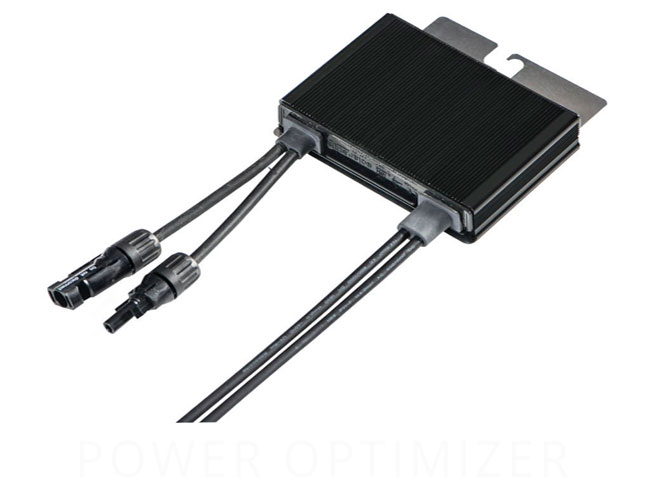
Maintenance – Roof versus Ground Mounted
- Roof-mounted solar systems have no moving parts and require little maintenance. Clean leaves and debris from panels when needed.
- Ground mounted systems with automatic or manual operated trackers will require maintenance. Generally, ground mount solar panels cost more than rooftop solar on a per-watt basis because of additional labor and permitting that may be required for the installation. But if your roof size/angles are inadequate and you have the land space, a ground mounted system is a consideration.
Protect your Solar Array from Damaging Surges
Solar systems’ exposure to lightning-induced surges increases the potential for damage to your system and/or home. For this reason, SECO Energy recommends that members who own, or are contemplating the installation of a solar system, incorporate quality surge protection devices (SPDs) into the design. The number of SPDs required will depend upon the size, complexity, and specific technology of the solar system. Those with battery storage and/or backup generators require SPDs for each installed interface. Key considerations when applying SPDs should include the protection of the software to the residence and the inverter from both the solar direct current (DC) input and the alternating current (AC) transfer switch plus all references/connections to the site’s ground should also be protected. The easiest, safest and most cost-effective way of doing this is to employ SPDs on the mounting back panel/plane used to hold the inverter/charger system. For installations utilizing micro-inverter technology, protect the AC connections to the electric distribution system. Note National Electric Code(s) requires all SPDs are ANSI/UL 1449 rated. Direct current (DC) SPDs for inverters must be specifically labeled for that application. If you cannot confirm the SPDs meet these specifications, do not use the product.
Surge protection for solar systems will vary widely between designs and product types. Thus, you should consult your contractor when developing a surge protection plan.